In Rajasthan, a very small village by the name of Akola has been, for hundreds of years, linked with a unique block printing design — dabu. It is mentioned that it replicates the colors of the sky — blue of the working day, indigo of the evening, and the crimson hues of a sunset.
Its origins are debated — some say it designed its way to Rajasthan from China in 675 Advert, and some declare it originated in the desert location — but in excess of time, Akola has turn out to be just about synonymous with this art, which works by using organic materials from the earth to create intricate styles.
There was a time when dabu printing was prevalent throughout Rajasthan, but Akola is presently among the the several remaining hubs of the art. Right now, the seventh era of these artisans operate below.
Any one who visits this community is bound to be captivated by the indigo hues and character influenced motifs. Alka Sharma, a textile designer from Alwar, felt no unique when she to start with visited the village in 2007.
“I completed my graduate reports in textile building in 2003 and was looking to function with artisans in Rajasthan. I had generally read of the area of Akola, well-known for artisan people who devoted their life to preserving prints, and considered this would be a fantastic chance for me. So in 2007, I made a decision to stop by,” she tells The Improved India.
She provides that her intent at the time wasn’t to get started a brand, but relatively to have an understanding of textiles and assist widen their scope.
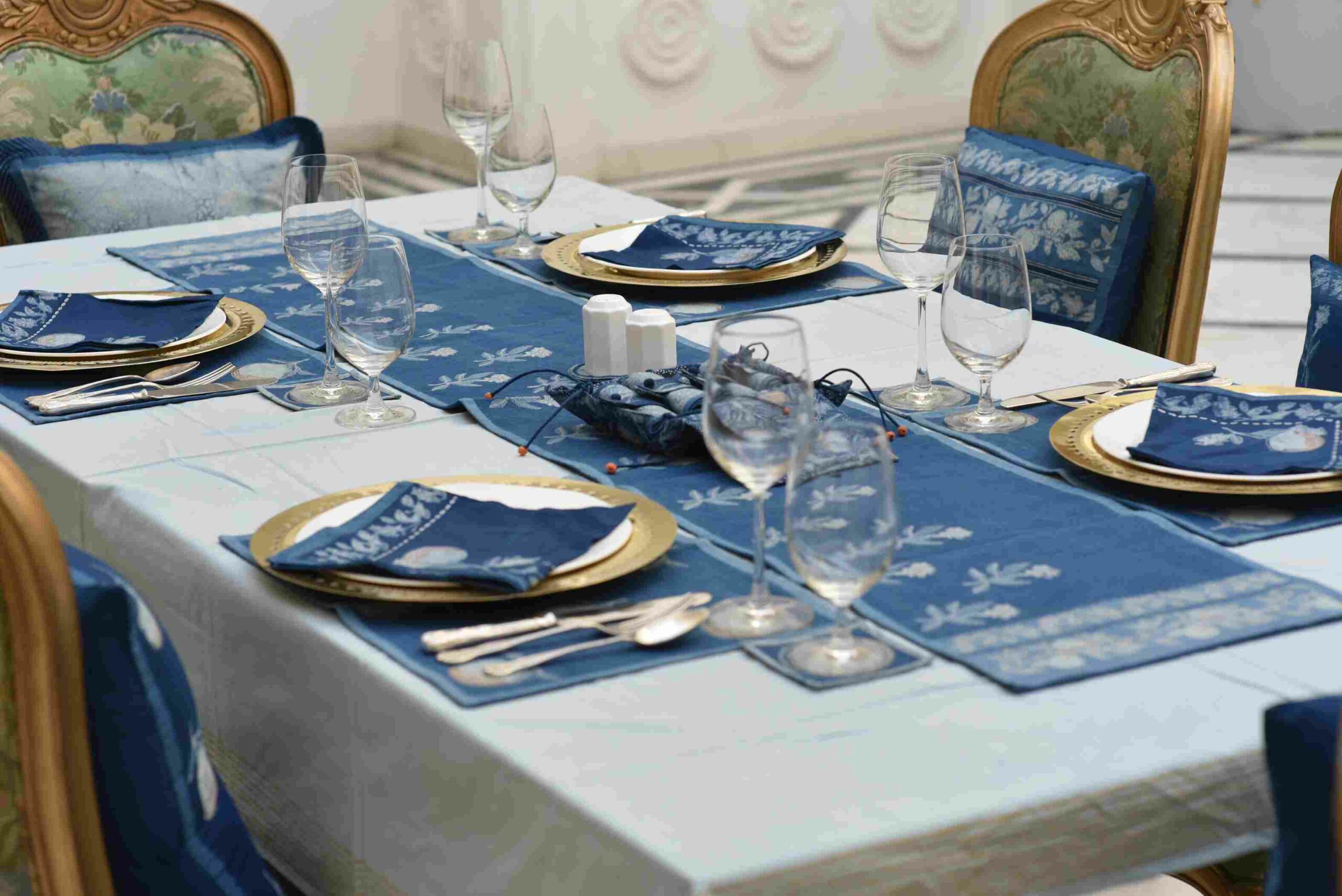
But, on investing a couple days at the Akola village, Alka suggests she did not have the heart to permit this knowledge close.
“I learnt so substantially even though in Akola. Whilst nowadays there are numerous households effectively versed with the art, at the time, there was only a single loved ones engaged in it. They were properly-to-do and more importantly possessed a desk (a requirement in dabu printing). I required additional families to be involved so they could earn by it,” she notes.
A heritage brand is born in Udaipur
The up coming number of months were filled with experiments and tough get the job done, as Alka labored with 200 girls artisans to type self-aid teams. She herself learnt the dabu artwork form and qualified the gals in it. She states that when they did not have an indigo dye bath then, they would handle with tiny tanks and buckets.
Her work was supported by a scheme by the Ministry of Textiles, and she was also joined by master craftsmen from Jaipur.
The enthusiasm to engage in dabu artwork shortly turned into an thought for a manufacturer, and Aavaran was born in 2012.
The brand name was an try by Alka to “revive and maintain the classic craft of dabu”. She provides that while undertaking this, she also preferred to make certain economic empowerment of the indigenous craft persons in the region.
Reminiscing about the journey right until now, Alka states it has been surreal. “I hardly ever assumed I would have a brand name sometime. When I started off perform with the artisans I did so with the aim of having the craft to a further level. There was a ton of brainstorming,” she notes.
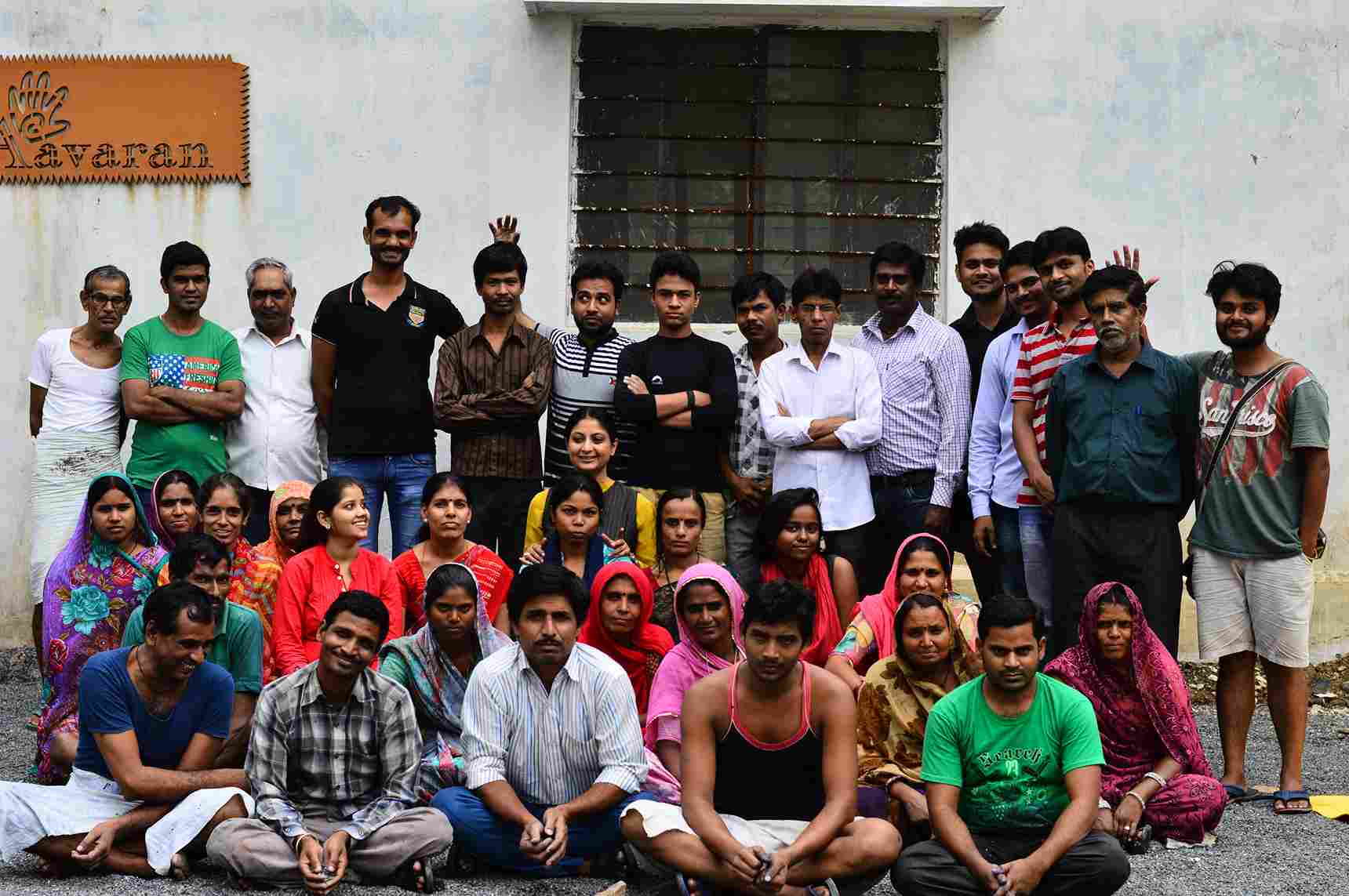
On the other hand, when accomplishment was all around the corner, so was a conflict.
“I wanted to contain artisans from minimal-revenue groups. But the properly-to-do artisans, who have been by now engaged in dabu printing, did not like it, as they thought it was a danger to their small business. This caused a divide,” she provides.
In 2015, Alka along with the artisans she had collected and mentored by way of the yrs, moved to Udaipur where by they started their very first keep.
“Our perform spoke for by itself. Folks commenced noticing our prints and approaching us,” she adds, attributing the reason for all the love they obtained to the timelessness of the dabu design.
“It is painstaking to produce but beautiful all the very same.”
Wet mud, gum and wheat chaff
The dabu printing procedure is a adore affair between three issues — mud from the desert, water from the river, and blocks carved by skilled artisans in the area.
Wondering again to the very first-ever selection she did — a backdrop of Lord Krishna — Alka calls it “traditional and simple”, but with a “tedious” method.
“Mud is gathered from the lakeside and stored in a tank right away. The damp mud is then combined with glue from the babool tree, beedan (wheat chaff) and chuna (limestone) to get ready a paste regularity and the blend is sieved. A woodblock is then dipped into the paste and placed on to the cloth, which has been washed and dried to take out the starch,” she notes.
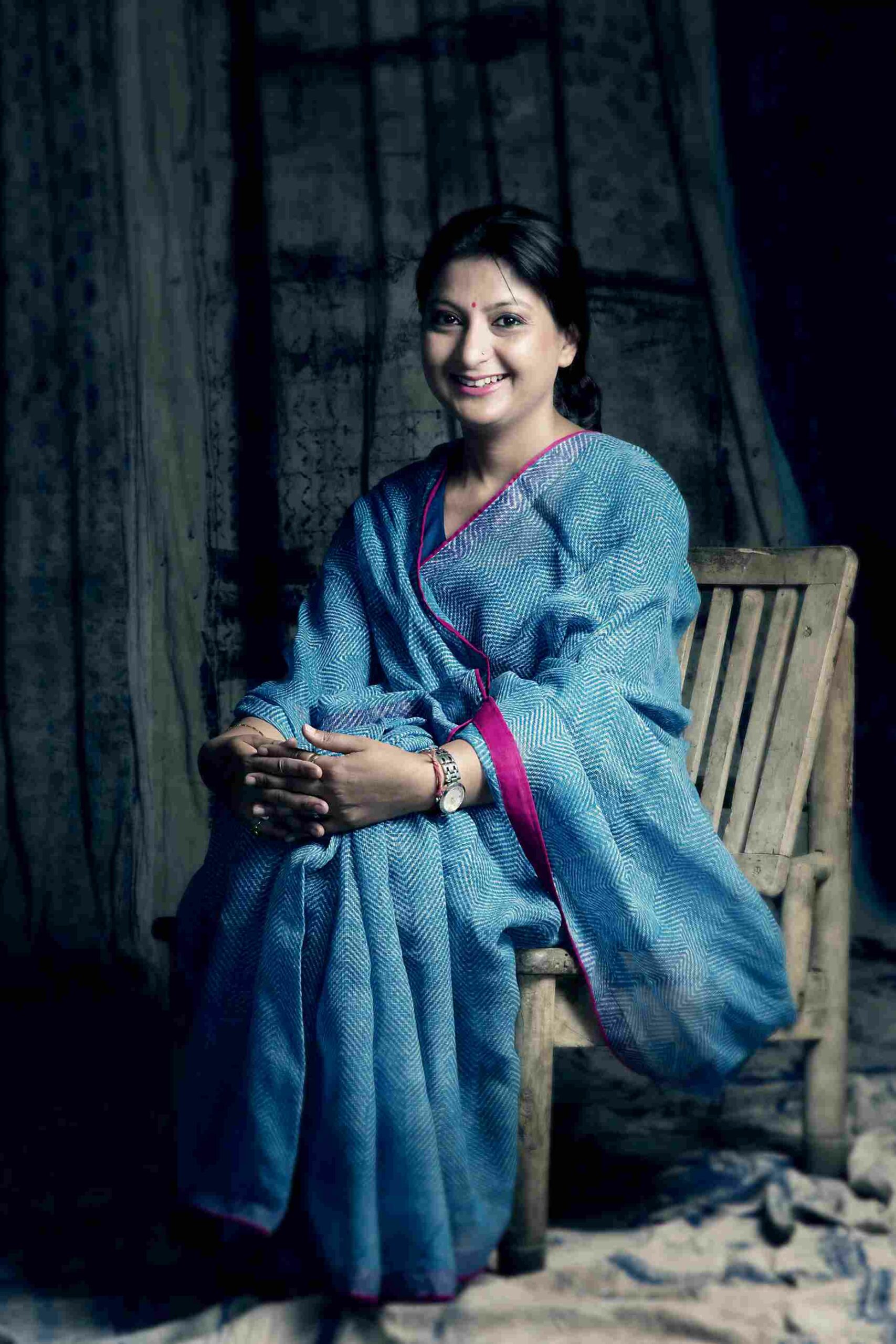
On the areas of the fabric where the paste lies, sawdust is from time to time used to avoid color penetration throughout the dyeing procedure. The upcoming stage is to dip the cloth into a cauldron dye. This can be carried out at the time or several moments as wished-for. When the fabric is taken off from the dye tank, the end result is reached — a cloth dyed in the wished-for color, with blank areas in in between, that create the illusion of motifs.
The dye does not capture on in these areas, as the mud-resistant block print has been utilised here.
When the traditional dabu printing design and style will involve the use of indigo dye, Aavaran has expanded this to other vegetable dyes to develop vivid hues. “The reason the procedure is prolonged is since a fresh batch of paste demands to be organized each individual day,” explains Alka, noting that the resultant item, on the other hand, is truly worth the work.
“It is a sustainable fabric, good for the skin — as it is made up of purely natural dyes — and the atmosphere — as when washed, the dyes do not leach into the drinking water,” she provides.
A protected area for artisans to stand on their ft
These days, Aavaran operates with 100 in-house artisans in its 40,000 sq ft manufacturing house.
“Each artisan specialises in a unique action. For some this could be stitching, for other people it is patchwork or printing,” clarifies Alka. “We also assist a lot more than 200 girls across 4 villages. They are paid a stipend of Rs 15,000 to 40,000 just about every thirty day period.”
A person of the artisans, Poonam, has been functioning with the brand name due to the fact 2007. She states it has served her maintain her spouse and children. “I have been equipped to give my child with the best instruction achievable mainly because of the work and also have my own house,” she says.
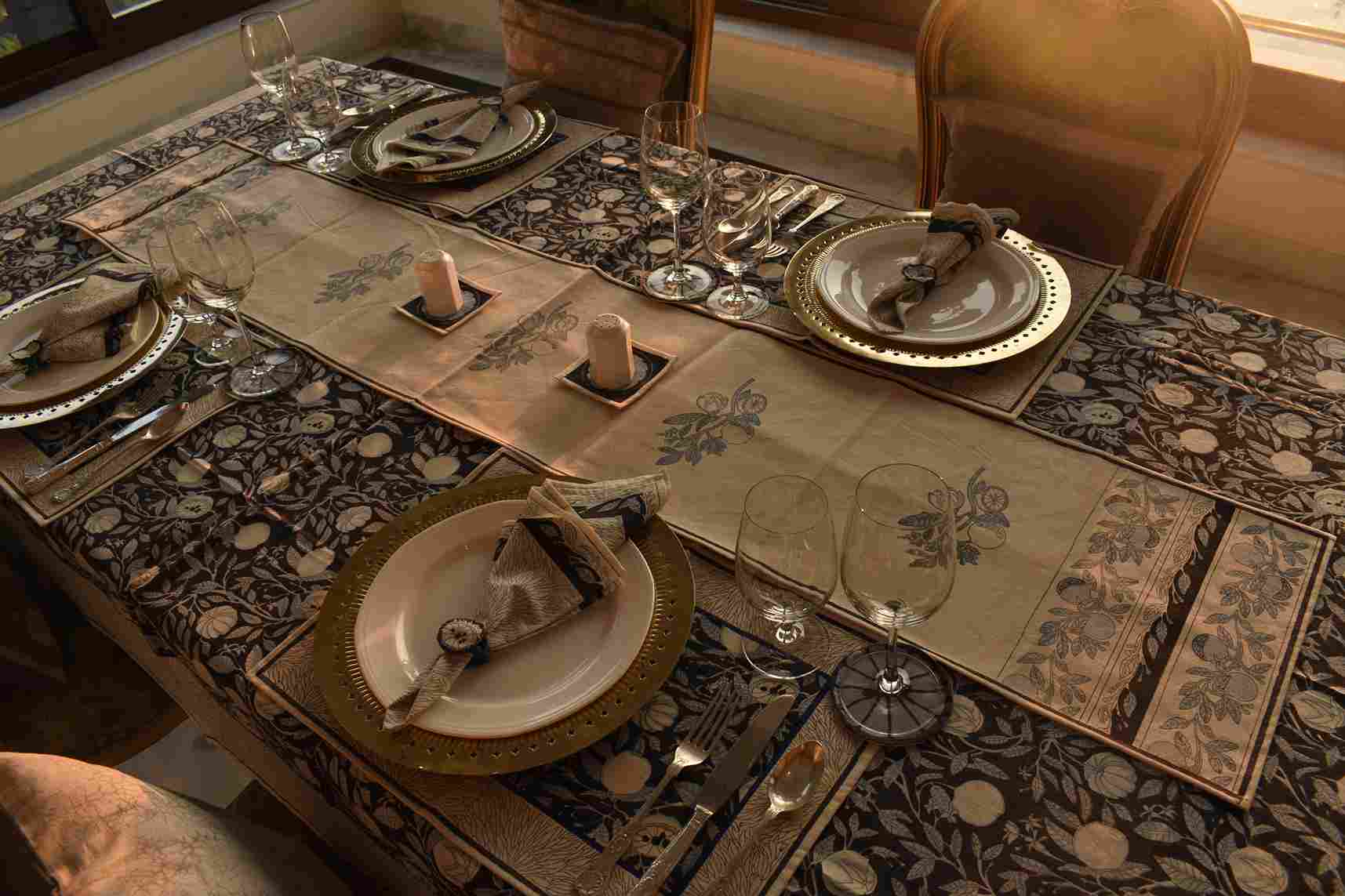
Another artisan Prabhat, who joined Aavaran in 2015, states he arrived to Udaipur from West Bengal with the intention of inspecting and chopping fabric, but has now figured out a diverse number of abilities. “At Aavaran I learnt all the things like dyeing, printing, and generation management. At this time, I control manufacturing and on the lookout after textiles,” he adds.
When the magic of dabu is established in Udaipur, clients pan India can order the collections on-line.
This features lehengas, tunics, kurtas, shirts and extras made of squander cloth such as baggage, pouches and potlis, jewellry manufactured with cloth scraps jutis and much more. Aavaran sees all around 14,000 orders quarterly and has witnessed a turnover of Rs 3 crore in the previous monetary yr, says Alka.
As Alka is occupied churning out orders to fulfill the requires of the festive period, she suggests life could not have turned out much better. “While I commenced out with the intent of mastering a new print style and helping protect it, I managed to produce some thing that I never ever thought achievable. Dabu artwork is the delight of my location.”
You can have the magic of dabu artwork shipped to your residence, below.